raw material
Carbon Steel, Nickel Alloy, Stainless Steel, Duplex, Super Duplex
Based on customers’ needs, all utilized materials of the products of GAZAR brand have so far been carbon steel, nickel alloy, stainless steel, duplex, super duplex.
1. Carbon steel
- ASTM A105, A105N
- ASTM A216 WCB, WCC
- ASTM A217 WC6, WC9,CW6, C12
- ASTM A350 LF2, LF3, LF6
- ASTM A352 LCB, LCC, LC3
- ASTM A694 F52, F60, F65
2. Stainless steel, Duplex, Super Duplex
- ASTM A182 F11, F20, F22, F304/F304L, F316/F316L, F316H, F316Ti, F321, F347, F347H, F44
- ASTM A182 F5, F51, F52, F53, F55
- ASTM A182 F60, F65, F6A, F6B, F6NM F9, F91, FXM19
- ASTM A276/A479 304/304L, 316/316L, 316H, 316Ti, 321, 347, 347H, 904L
- ASTM A351 CK3MCuN, CA15, CF8, CF3, CF8M, CF3M, CG8M, CF8C
- ASTM A479 S31254, S31803, S20910, S32750, S32760, S41000, S41400, S41300, S17400
- ASTM A479 S31803, S32750, S32760, S20910, S41000, S41400, S41300, S17400
- ASTM A739 B11, B22
3. Nickel Alloys
- ASTM N08825, N06625, N04400, N08020, N07750, N07718, N08926, N07725, N05500
- Not listed materials are available upon request.
Valve Applications:
Since the application and the process fluid characteristics are given by the customer are the main factors in selecting a valve type and construction materials, this is considered very important in designs. While clean fluids generally allow a wide range of valves and materials, for dirty fluids and high-risk applications the choice is limited to a few valve types and selected materials.
- Hydrocarbons (Oil, Gas, derivatives)
- Utility (Water, Air, Nitrogen, Hydraulic Oils)
- Corrosive & Dirty (severe abrasive services in Sour, Sandy, Slurry, Fouling, Solidifying conditions)
- High Temperature (≤ 1000°C)
- Low Temperature (-45°C < t > 0°C)
- High Pressure (≤ 1500 bar)

The Control and Quality Guarantee System:
All input and output equipment of the factory are examined by the control and quality guarantee team of the company and tested and verified by the existing apparatuses. In this respect, some services are outsourced, and thus we appreciate our cooperator laboratories for their partnerships.
Due to the fact that valves have a direct impact on the proper operation of infrastructure and the continuous production process in the industry, quality control and inspection of industrial valves is considered an important issue. Leaks or problems in this sector can disrupt the production or service cycle in these industries or cause accidents. Industrial valves reduce pressure, regulate flow or protect the transmission process. Therefore, it is obvious that the efficiency of sensitive centers such as petrochemicals, refineries, power plants and other industries, whether in terms of output, reliability or proper operation, are directly affected by the performance of valves.
For this reason, different standards for testing and inspection of industrial valves have been introduced by various organizations. These standards are necessary to ensure compliance of valves with technical requirements, process conditions and environmental regulations. These standards also help engineers in the selection process on items such as material, pressure classification and temperature. The following are some of the essential and optional tests in the production of valves:
- Shell test
- Backseat test
- Low-pressure closure test
- High-pressure closure test
- Visual examination of castings
- High-pressure pneumatic shell test
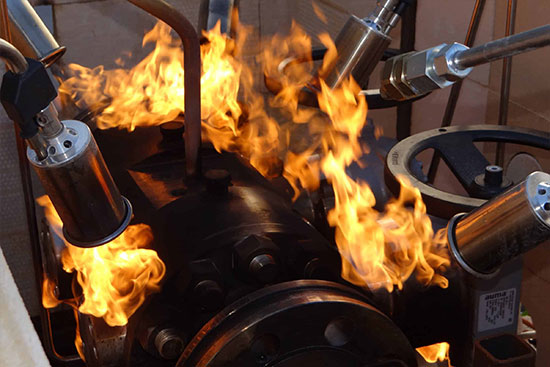
Valve Leak Testing:
The Sadra Mahan Parsian Company has its own in-house testing department and the following valve leak testing can be internally performed by qualified and experienced personnel:
- Hydrostatic shell & seat test;
- Low-pressure gas test (with air or Nitrogen) according to Annex B of API 6D, API 598, EN 12266-1 or to customer-specific requirements;
- Fugitive emission gas test (with Helium) according to test to ISO 15848 /2
- Cavity relief test
High-temperature tests can be arranged according to Customer’s requests
Specific Customer’s requirements in terms of special testing, pressures, durations, and acceptance criteria can be evaluated and incorporated into our products.
Available Material Destructive Examinations:
The following destructive examinations can be also performed according to the customer and the project requirements:
- Mechanical and Impact test down to –196°C
- Chemical analysis check
- Corrosion tests
- Micro examinations by electronic microscope up to 500x magnifications
- Hydrogen-Induced Cracking test (HIC) & Sulphide Stress Corrosion Cracking (SSCC)
Available Material Non-Destructive Examinations:
The following Non-Destructive Examinations are performed by qualified personnel, certified in accordance with EN 473-ISO 9712 or SNT-TC-1A LEVEL 2:
- MT (Magnetic particle examination)
- UT (Ultrasonic examination)
- PT (Dye penetrant examination)
- RT (Radiographic test)
- PMI (Positive material identification)
- Hardness test